How Manitowoc is Harnessing Data and Empowering Efficiency with Telematics
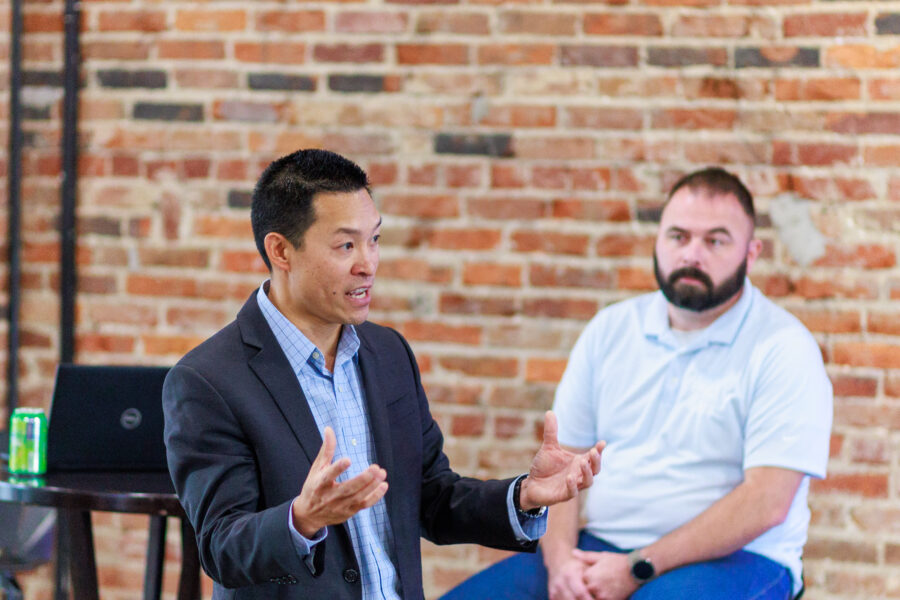
One of Fleet Cost & Care’s (FCC) manufacturer partners, Manitowoc, joined us at our latest Leadership Summit. Matthew Wong, the VP of Customer Support was in attendance, and wanted to share with a wider audience what Manitowoc is doing to advance data capture and data leveraging with their machines to benefit its customers and FCC users. Take it away Matt!
The vibrant atmosphere and palpable excitement surrounding Indianapolis in the month of May prior to the Indy 500 was impossible to overlook. That same energy was present at Fleet Cost & Care’s third Leadership Summit which included a distinguished assembly of crane industry partners and customers began. Fittingly, the group used the ‘RACE’ acronym to signify the transformative potential of data across various aspects of business. By incorporating data-driven practices related to Results, Analysis, Collaboration, and Evaluation, companies can unlock new levels of efficiency, safety, and profitability, propelling their success in an increasingly data-centric world. In this area Manitowoc knows there is an important role to play for our customers. Here is what we have been up to:
Rely on the Data
Manitowoc, a global crane manufacturer of Potain, Manitowoc, Grove, and National branded cranes, recently launched our next generation telematic system, Potain Connect and Grove Connect. It provides crane machine data, such as fuel and DEF fluid levels, active and critical fault codes, and machine working status, for fleet manager and service personnel, so they can rely on near-real time data when managing their fleet of machines.
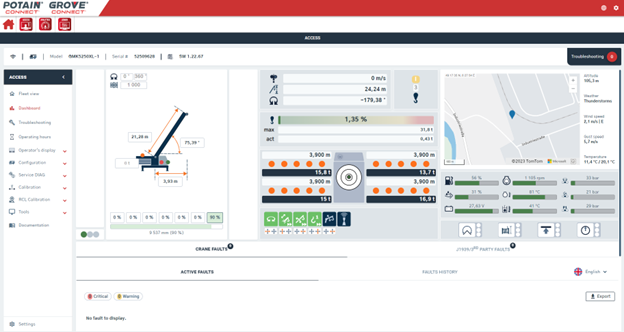
Potain Connect & Grove Connect, will provide a wealth of data to the crane owner.
Accountability of Process
Machine data has the potential for better traceability and accountability, as you can monitor the current conditions and review previous history. It can lead to training opportunities, proactive machine maintenance, and better planning through iterative learning.
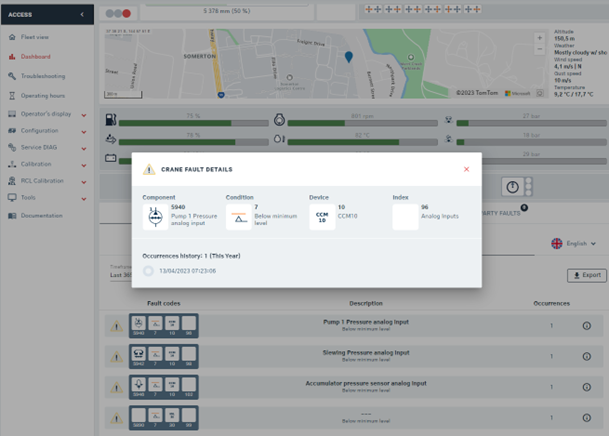
Data captured can be used to monitor maintenance schedules, learning opportunities, and more.
Certification of Results
Potain Connect and Grove Connect are developing analytic reports, such as machine utilization and greenhouse gas emissions summary, to certify the results and expected outcomes from the machine and operation. Manitowoc is also working toward a data API that would allow customers to access their data in a cleansed and structured format for their own custom reporting and data analytics.
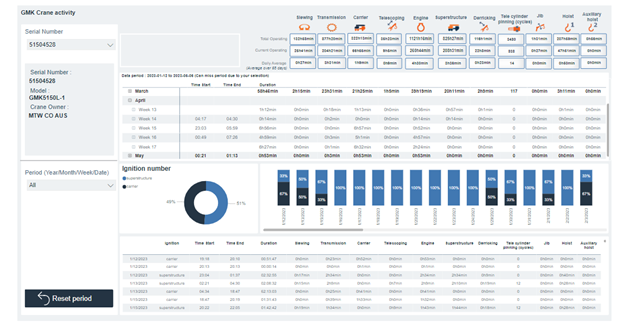
Machine data can be displayed in easy to interpret dashboards, so you can make informed decisions.
Execute
For crane rental customers with FCC’s software, many operations are executed using NexGen or Atom. Manitowoc is working with FCC to evaluate a secure data exchange that will provide useful data to FCC customers enabling operations to be enhanced and streamlined.
For example, telematic data, such as location and machine hours, can automatically update and populate FCC’s NexGen at the unit level. Machine fault codes, upon verification and definition of business rules, can trigger a work order and dispatch a technician to the machine. The machine’s utilization and working conditions profile can provide insights for operator training and job planning.
To conclude, the utilization of telematics to harness machine data will undoubtedly yield advantages for crane customers and enhance customer services. However, data without context will eventually have limitation to the use case. That is why collaborating with Fleet Cost & Care and other digital partners in the crane industry will be crucial to delivering the full value of the digital ecosystem to our customers.